On the Economy of Machinery and Manufactures - Charles Babbage (interesting books to read in english .TXT) 📗
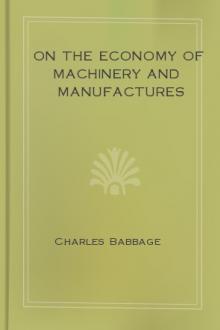
- Author: Charles Babbage
- Performer: -
Book online «On the Economy of Machinery and Manufactures - Charles Babbage (interesting books to read in english .TXT) 📗». Author Charles Babbage
to the calico. The substance of the cloth is pressed very
forcibly into the cavities thus formed, and retains its pattern
after considerable use. The watered appearance in the cover of
the volume in the reader’s hands is produced in a similar manner.
A cylinder of gun-metal, on which the design of the watering is
previously cut, is pressed by screws against another cylinder,
formed out of pieces of brown paper which have been strongly
compressed together and accurately turned. The two cylinders are
made to revolve rapidly, the paper one being slightly damped,
and, after a few minutes, it takes an impression from the upper
or metal one. The glazed calico is now passed between the
rollers, its glossy surface being in contact with the metal
cylinder, which is kept hot by a heated iron enclosed within it.
Calicoes are sometimes watered by placing two pieces on each
other in such a position that the longitudinal threads of the one
are at right angles to those of the other, and compressing them
in this state between flat rollers. The threads of the one piece
produce indentations in those of the other, but they are not so
deep as when produced by the former method.
122. Embossing upon leather. This art of copying from
patterns previously engraved on steel rollers is in most respects
similar to the preceding. The leather is forced into the
cavities, and the parts which are not opposite to any cavity are
powerfully condensed between the rollers.
123. Swaging. This is an art of copying practised by the
smith. In order to fashion his iron and steel into the various
forms demanded by his customers, he has small blocks of steel
into which are sunk cavities of different shapes; these are
called swages, and are generally in pairs. Thus if he wants a
round bolt, terminating in a cylindrical head of larger diameter,
and having one or more projecting rims, he uses a corresponding
swaging tool; and having heated the end of his iron rod, and
thickened it by striking the end in the direction of the axis
(which is technically called upsetting), he places its head upon
one part of the lage; and whilst an assistant holds the other
part on the top of the hot iron, he strikes it several times with
his hammer, occasionally turning the head one quarter round. The
heated iron is thus forced by the blows to assume the form of the
mould into which it is impressed.
124. Engraving by pressure. This is one of the most beautiful
examples of the art of copying carried to an almost unlimited
extent; and the delicacy with which it can be executed, and the
precision with which the finest traces of the graving tool can be
transferred from steel to copper, or even from hard steel to soft
steel, is most unexpected. We are indebted to Mr Perkins for most
of the contrivances which have brought this art at once almost to
perfection. An engraving is first made upon soft steel, which is
hardened by a peculiar process without in the least injuring its
delicacy. A cylinder of soft steel, pressed with great force
against the hardened steel engraving, is now made to roll very
slowly backward and forward over it, thus receiving the design,
but in relief. The cylinder is in its turn hardened without
injury., and if it be slowly rolled to and fro with strong
pressure on successive plates of copper, it will imprint on a
thousand of them a perfect facsimile of the original steel
engraving from which it was made. Thus the number of copies
producible from the same design may be multiplied a
thousand-fold. But even this is very far short of the limits to
which the process may be extended. The hardened steel roller,
bearing the design upon it in relief may be employed to make a
few of its first impressions upon plates of soft steel, and these
being hardened become the representatives of the original
engraving, and may in their turn be made the parents of other
rollers, each generating copperplates like their prototype. The
possible extent to which facsimiles of one original engraving may
thus be multiplied, almost confounds the imagination, and appears
to be for all practical purposes unlimited.
This beautiful art was first proposed by Mr Perkins for the
purpose of rendering the forgery of bank notes a matter of great
difficulty; and there are two principles which peculiarly adapt
it to that object: first, the perfect identity of all the
impressions, so that any variation in the minutest line would at
once cause detection; secondly, that the original plates may be
formed by the united labours of several artists most eminent in
their respective departments; for as only one original of each
design is necessary, the expense, even of the most elaborate
engraving, will be trifling, compared with the multitude of
copies produced from it.
125. It must, however, be admitted that the principle of
copying itself furnishes an expedient for imitating any engraving
or printed pattern, however complicated; and thus presents a
difficulty which none of the schemes devised for the prevention
of forgery appear to have yet effectually obviated. In attempting
to imitate the most perfect banknote, the first process would be
to place it with the printed side downwards upon a stone or other
substance, on which, by passing it through a rolling-press, it
might be firmly fixed. The next object would be to discover some
solvent which should dissolve the paper, but neither affect the
printing-ink, nor injure the stone or substance to which it is
attached. Water does not seem to do this effectually, and perhaps
weak alkaline or acid solutions would be tried. If, however, this
could be fully accomplished, and if the stone or other substance,
used to retain the impression, had those properties which enable
us to print from it, innumerable facsimiles of the note might
obviously be made, and the imitation would be complete. Porcelain
biscuit, which has recently been used with a black lead pencil
for memorandum books, seems in some measure adapted for such
trials, since its porosity may be diminished to any required
extent by regulating the dilution of the glazing.
126. Gold and silver moulding. Many of the mouldings used by
jewellers consist of thin slips of metal, which have received
their form by passing between steel rollers, on which the pattern
is embossed or engraved; thus taking a succession of copies of
the devices intended.
127. Ornamental papers. Sheets of paper coloured or covered
with gold or silver leaf, and embossed with various patterns, are
used for covering books, and for many ornamental purposes. The
figures upon these are produced by the same process, that of
passing the sheets of paper between engraved rollers.
Of copying by stamping
128. This mode of copying is extensively employed in the
arts. It is generally executed by means of large presses worked
with a screw and heavy flywheel. The materials on which the
copies are impressed are most frequently metals, and the process
is sometimes executed when they are hot, and in one case when the
metal is in a state between solidity and fluidity.
129. Coins and medals. The whole of the coins which circulate
as money are produced by this mode of copying. The screw presses
are either worked by manual labour, by water, or by steam power.
The mint which was sent a few years since to Calcutta was capable
of coining 200,000 pieces a day. Medals, which usually have their
figures in higher relief than coins, are produced by similar
means; but a single blow is rarely sufficient to bring them to
perfection, and the compression of the metal which arises from
the first blow renders it too hard to receive many subsequent
blows without injury to the die. It is therefore, after being
struck, removed to a furnace, in which it is carefully heated
red-hot and annealed, after which operation it is again placed
between the dies, and receives additional blows. For medals, on
which the figures are very prominent, these processes must be
repeated many times. One of the largest medals hitherto struck
underwent them nearly a hundred times before it was completed.
130. Ornaments for military accoutrements, and furniture.
These are usually of brass, and are stamped up out of solid or
sheet brass by placing it between dies, and allowing a heavy
weight to drop upon the upper die from a height of from five to
fifteen feet.
131. Buttons and nail heads. Buttons embossed with crests or
other devices are produced by the same means; and some of those
which are plain receive their hemispherical form from the dies in
which they are struck. The heads of several kinds of nails which
are portions of spheres, or polyhedrons, are also formed by these
means.
132. Of a process for copying, called in France clichee. This
curious method of copying by stamping is applied to medals, and
in some cases to forming stereotype plates. There exists a range
of temperature previous to the melting point of several of the
alloys of lead, tin, and antimony, in which the compound is
neither solid, nor yet fluid. In this kind of pasty state it is
placed in a box under a die, which descends upon it with
considerable force. The blow drives the metal into the finest
lines of the die, and the coldness of the latter immediately
solidifies the whole mass. A quantity of the half-melted metal is
scattered in all directions by the blow, and is retained by the
sides of the box in which the process is carried on. The work
thus produced is admirable for its sharpness, but has not the
finished form of a piece just leaving the coining-press: the
sides are ragged, and it must be trimmed, and its thickness
equalized in the lathe.
Of copying by punching
133. This mode of copying consists in driving a steel punch
through the substance to be cut, either by a blow or by pressure.
In some cases the object is to copy the aperture, and the
substance separated from the plate is rejected; in other cases
the small pieces cut out are the objects of the workman’s labour.
134. Punching iron plate for boilers. The steel punch used
for this purpose is from three-eighths to three-quarters of an
inch in diameter, and drives out a circular disk from a plate of
iron from one-quarter to five eighths of an inch thick.
135. Punching tinned iron. The ornamental patterns of open
work which decorate the tinned and japanned wares in general use,
are rarely punched by the workman who makes them. In London the
art of punching out these patterns in screw-presses is carried on
as a separate trade; and large quantities of sheet tin are thus
perforated for cullenders, wine-strainers, borders of waiters,
and other similar purposes. The perfection and the precision to
which the art has been carried are remarkable. Sheets of copper,
too, are punched with small holes about the hundredth of an inch
in diameter, in such multitudes that more of the sheet metal is
removed than remains behind; and plates of tin have been
perforated with above three thousand holes in each square inch.
136. The inlaid plates of brass and rosewood, called buhl
work, which ornament our furniture, are, in some instances,
formed by punching; but in this case, both the parts cut out, and
those which remain, are in many cases employed. In the remaining
illustrations of the art of copying by punching, the part made
use of is that which is punched out.
137. Cards for guns. The substitution of a circular disk of
thin card instead of paper, for retaining in its place the charge
of a fowling-piece, is attended
Comments (0)