Launch on Need by Daniel Guiteras (small books to read txt) 📗
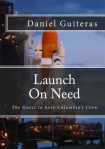
- Author: Daniel Guiteras
Book online «Launch on Need by Daniel Guiteras (small books to read txt) 📗». Author Daniel Guiteras
As the group quieted, Senca continued. “The team examined all available hi-res video and film. And as most of you know, the available imaging was quite limited for this launch. The external tank separation as visualized and filmed by the crew offered no help, either.” Senca was referring to how during all Shuttle launches, a member of the crew uses a handheld camcorder, on this mission a Sony PD-100, to film the external tank separation as viewed through the orbiter’s flight deck windows.
“We weren’t able to appreciate the bi-pod area of the external tank from the edited 35 seconds of video footage the crew downloaded to us. We had the crew download the rest of the footage from ET sep [external tank separation], but it gave us no more information, because the ET section of the tank in question had already rotated out of view.
“Using the orbiter’s hatch [the external door where the crew enters the orbiter before a launch] as a reference, we estimated the blob dimensions as shown on this slide, roughly the size of a small suitcase. The foam insulation covering the left bi-pod area, while still attached to the external tank and traveling with the shuttle, was moving at 2,300 feet per second [1,568 mph]. At Launch-plus-81.7 seconds, with the shuttle at an altitude of 65,860 feet, a chunk of bi-pod foam broke free from the external tank. During the 0.161 seconds between when the foam left the external tank and when it struck the orbiter’s left wing, the debris blob, with its low ballistic coefficient, decelerated from 2,300 to about 1,500 feet per second [or 1,568 to about 1,022 mph].
“Essentially, Columbia then smashed into the slowing foam debris at 546 miles per hour.”
Senca had their attention now. He advanced to the next slide, which contained a short computer-animation movie showing how the debris left the external tank and fell toward Columbia’s left wing. “We used computational fluid dynamics modeling software,” Senca said, clicking the play button on the computer screen to start the animation, “to study the airflow around the external tank and orbiter, and to learn how that airflow would affect the falling debris. Our best estimates at this time show the debris striking the wing between RCC panels 6 through 9 along the leading edge of the left wing.”
Everyone in the room, even the youngest and least experienced NASA employees, knew the function of the RCC panels. There were 22 uniquely shaped panels that ran the length of each wing and served as a protective cap. Senca advanced to his next slide, showing the RCC panels for audience orientation.
NASA graphic, CAIB Report Vol. I, Page 55
Referred to widely as RCC panels, the Reinforced Carbon-Carbon panels were manufactured through a complicated multistep process using layers of laminated graphite-impregnated rayon fabric and impregnated resins. The final step of fabrication involved firing the panels in a furnace, like clay in a kiln, to 3,000 degrees Fahrenheit. The panels were a critical component of the orbiter’s thermal protection system, and could tolerate a temperature range from minus-250 to 3,000 degrees Fahrenheit. They were numbered beginning with “1” at the inboard aspect of the wing, closest to the fuselage, on up to “22” at the outside wing tip.
“The angle of incidence is very important here,” Senca continued, advancing to his next slide, which showed a cross section diagram of the wing’s leading edge. “If the debris hits at the underside of the curve, nearly parallel to the lower plane of the wing, then the damage is minimal. Our video review, however, and airflow modeling suggest that the debris hit the wing close to the center of the leading edge, thereby nearly doubling the force of impact.”
After Senca showed his last slide, which summarized the team’s findings, he fielded multiple questions and challenges about how the numbers and estimates were obtained. In response to those who thought the debris strike represented nothing more than a turnaround issue—something to be refurbished after landing, an expert in the orbiter’s thermal protection system assisted Senca by saying, “Don’t forget the design requirements of the RCC panel: They only have to withstand the kinetic energy of a 0.006 foot-pound impact. From the video analysis, it appears the debris strike may have well exceeded those design specifications.”
But no matter what questions were raised, no matter the perspective, the discussion always returned the same result.
“We could go on all day about this,” Senca said, “speculating this and that, arguing one method of modeling over another. But we keep coming back to the same point. There’s no way for us to know for sure what damage the wing has sustained, no way for us to tell for sure from the limited imaging we have. And that is why the tiger team is recommending we obtain outside imaging of Columbia on orbit immediately, using either satellite or ground-based resources.”
“Thank you, Joe, and your team as well, for your work on this,” Pollard said as she stood once again to redirect the meeting. “Outside imaging does sound plausible as indicated and based on your findings.” She looked to her left and right, polling the mission management team members. They nodded in agreement. “Okay, then, without any objection from the team,” Pollard continued, “following this meeting we will make the necessary contacts with Cheyenne Mountain to see about getting imaging of Columbia’s wing.
“There is something else I think we should be planning for,” Pollard said, “something we should keep in mind.” She looked down to her immediate left, to the Space Shuttle Program Manager, her boss and mentor, Reid Hamilton. He nodded, not sure what she had in mind, but trusting her nonetheless. Pollard moved around her chair and walked over
Comments (0)