Things To Make - Archibald Williams (the reader ebook .TXT) 📗
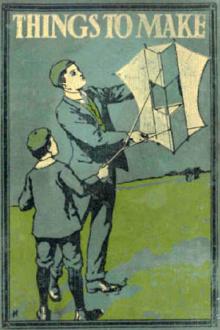
- Author: Archibald Williams
- Performer: -
Book online «Things To Make - Archibald Williams (the reader ebook .TXT) 📗». Author Archibald Williams
If you find the construction of the T-shaped rod too difficult, two courses are open—
(l) To get a carpenter to do the job for you, or
(2) To give the rod the triangular section shown in Fig. 129, each side of the equilateral triangle being half an inch long.
[Illustration: FIG. 150—Side elevation of model aeroplane.]
The top of the T or the base of the triangle, as the case may be, is used uppermost. This rod must be pierced in three places for the vertical masts employed in the bracing of the rod, trussing the main plane, and adjusting the elevator. These are spaced out in Fig. 130, which shows a side elevation of the model. Their sectional dimensions are 1/16 by 1/4 inch; their respective lengths are given in Fig. 130. Round the front edges and sharpen the rear.
In Fig. 130 is shown the correct attitude or standing pose necessary to make the model rise quickly and sweep boldly up into the air without skimming the ground for some 10 to 20 yards as so many models do. E is the elevator (7 by 3 inches); A the main plane (5-1/2 by 29 inches); W the wheels; and RS the rear skid, terminating in a piece of hooked steel wire. The vertical bracing of these masts is indicated. The best material to use for the purpose is Japanese silk gut, which is very light and strong. To brace, drill a small, neat hole in the mast and rod where necessary, pass through, and tie. Do the same with each one.
To return to the central mast, which must also form the chassis. This is double and opened out beneath as shown in Fig. 131, yz being a piece similar to the sides, which completes, the triangle x y z and gives the necessary rigidity. Attach this piece by first binding to its extremities two strips of aluminium, or by preference very thin tinned iron, Tl and T2. Bend to shape and bind to xy, xz as shown in Fig. 131.
[Illustration: FIG. 131.—Front elevation of chassis.]
[Illustration: FIG. l32.-Wheel for model aeroplane chassis.]
[Illustration: FIG. 133.—Plan of model aeroplane.]
The Wheels and Chassis.—WW are the two wheels on which the model runs. They are made of hollow brass curtain rings, 1 inch in diameter, such as can be bought at four a penny. For spokes, solder two strips of thin tinned iron to the rings, using as little solder as possible. (Fig. 132.) To connect these wheels with the chassis, first bind to the lower ends of xy, xz two strips of thin tinned iron, T3 and T4, after drilling in them two holes of sufficient size to allow a piece of steel wire of "bonnet pin" gauge to pass freely, but not loosely, through them. Soften the wire by making it red hot and allowing it to cool slowly, and solder one end of this wire (which must be quite straight and 5-1/4 inches long) to the centre of the cross pieces or spokes of one wheel. Pass the axle through the holes in the ends of xy, xz, and solder on the other wheel. Your chassis is then finished.
The rear skid (RS in Fig. 130) is attached to the central rod by gluing, and drilling a hole through both parts and inserting a wooden peg; or the upright may be mortised in. On no account use nail, tack, or screw. Attach the vertical masts and the horizontal ones about to be described by gluing and binding lightly with thread, or by neatly glued strips of the Hart's fabric used for the planes.
Horizontal Spars, etc.—To consider now the horizontal section or part plan of the model, from which, to avoid confusion, details of most vertical parts are omitted. Referring to Fig. 133, it will be seen that we have three horizontal masts or spars—HS1, 4 inches; HS2, 6 inches; and HS3, slightly over 12 inches long. The last is well steamed, slightly curved and left to dry while confined in such a manner as to conform to the required shape. It should so remain at least twenty-four hours before being fixed to the model. All the spars are attached by glue and neat cross bindings. If the central rod be of triangular instead of T section, the join can be made more neatly. The same remarks apply to the two 9 and 10 inch struts at the propeller end of the rod, which have to withstand the pull of the rubber motor on PPl. These two pieces will have a maximum strength and minimum weight if of the T section used for the rod. If the work is done carefully, 1/4 inch each way will be sufficient.
Main Plane and Elevator.—The framework of each plane is simply four strips of satin walnut or other suitable wood, 1/4 inch broad and 1/16 inch or even less in thickness for the main plane, and about 1/16 by 1/16 inch for the elevator. These strips are first glued together at the corners and left to set. The fabric (Hart's fabric or some similar very light material) is then glued on fairly tight—that is, just sufficiently so to get rid of all creases. The main plane is then fixed flat on to the top of the central rod by gluing and cross binding at G and H. (A better but rather more difficult plan is to fasten the rectangular frame on first and then apply the fabric.) The same course is followed in dealing with the elevator, which is fixed, however, not to the rod, but to the 4-inch horizontal spar, HS1, just behind it, in such a manner as to have a slight hinge movement at the back. This operation presents no difficulty, and may be effected in a variety of ways. To set the elevator, use is made of the short vertical mast, M1. A small hole is pierced in the front side of the elevator frame at Z, and through this a piece of thin, soft iron wire is pushed, bent round the spar, and tied. The other end of the wire is taken forward and wrapped three or four times round the mast M1, which should have several notches in its front edge, to assist the setting of the elevator at different angles. Pull the wire tight, so that the elevator shall maintain a constant angle when once set. H H1 is a piece of 25 to 30 gauge wire bent as shown and fastened by binding. It passes round the front of the rod, in which a little notch should be cut, so as to be able to resist the pull of the twin rubber motors, the two skeins of which are stretched between H H1 and the hooks formed on the propeller spindles. If all these hooks are covered with cycle valve tubing the rubber will last much longer. The rubber skeins pass through two little light wire rings fastened to the underside ends of HS2. (Fig. 133.)
The front skid or protector, FS, is made out of a piece of thin, round, jointless cane, some 9 inches in length, bent round as shown in Fig. 134, in which A B represents the front piece of the T-shaped rod and x y z a the cane skid; the portion x y passing on the near side of the vertical part of the T, and z a on the far side of the same. At E and F thread is bound right round the rod. Should the nose of the machine strike the ground, the loop of cane will be driven along the underside of the rod and the shock be minimized. So adjust matters that the skid slides fairly stiff. Note that the whole of the cane is on the under side of the top bar of the T.
[Illustration: FIG. 134.—Front skid and attachment to backbone.]
Bearings.—We have still to deal with the propellers and their bearings. The last, TN and TNl (Fig. 133), are simply two tiny pieces of tin about half a gramme in weight, bent round the propeller spar HS3 at B and B1. Take a strip of thin tin 1/4 inch wide and of sufficient length to go completely round the spar (which is 1/4 by 1/8 inch) and overlap slightly. Solder the ends together, using a minimum amount of solder. Now bore two small holes through wood and tin from rear to front, being careful to go through the centre. The hole must be just large enough to allow the propeller axle to run freely, but not loosely, in it. Primitive though such a bearing may seem, it answers admirably in practice. The wood drills out or is soon worn more than the iron, and the axle runs quite freely. The pull of the motor is thus directed through the thin curved spar at a point where the resistance is greatest—a very important matter in model aeroplane construction. To strengthen this spar further against torsional forces, run gut ties from B and Bl down to the bottom of the rear vertical skid post; and from B to B1 also pass a piece of very thin piano wire, soldered to the tin strips over a little wooden bridge, Q, like a violin bridge, on the top of the central rod, to keep it quite taut.
[Illustration: FIG. 135—"Centrale" wooden propeller.]
Propellers.—To turn now to the propellers. Unless the reader has already had fair experience in making model propellers, he should purchase a couple, one right-handed and one left-handed, as they have to revolve in opposite directions. It would be quite impossible to give in the compass of this article such directions as would enable a novice to make a really efficient propeller, and it must be efficient for even a decent flight with a self-launching model. The diameter of the two propellers should be about 11-1/2 to 11-3/4 inches, with a pitch angle at the extremities of about 25 to 30 degrees as a limit. The "centrale" type (Fig. 135) is to be preferred. Such propellers can be procured at Messrs. A. W. Gamage, Ltd., Holborn, E.C.; Messrs. T. W. K. Clarke and Co., Kingston-on-Thames; and elsewhere.
For the particular machine which we are considering, the total weight of the two propellers, including axle and hook for holding the rubber, should not exceed 3/4 oz. This means considerable labour in cutting and sandpapering away part of the boss, which is always made much too large in propellers of this size. It is wonderful what can be done by care and patience. The writer has in more than one case reduced the weight of a propeller by more than one-half by such means, and has yet left sufficient strength.
The combined axle and hook should be made as follows:—Take a piece of thin steel wire, sharpen one end, and bend it as shown at C (Fig. 136). Pass the end B through a tight-fitting hole in the centre of the small boss of the propeller, and drive C into the wood. Solder a tiny piece of 1/8-inch brass tubing to the wire axle at A, close up to the rubber hook side of the propeller, and file quite smooth. The only things now left to do are to bend the wire into the form of a hook (as shown by the dotted line), and to cover this hook, as already advised, with a piece of valve tubing to prevent fraying the rubber skeins.
[Illustration: FIG. 136.—Axle and hook for propeller.]
Weight.—The weight of a model with a T-shaped central rod 1/16 inch thick should be 4-1/2 oz. Probably it will be more than this—as a maximum let us fix 6 oz.—although 4-1/2 oz. is quite possible, as the writer has proved in actual practice. In any case the centre of gravity of the machine without the rubber motor should be situated 1 inch behind the front or entering edge of the main plane. When the rubber motor (14 strands of 1/16-inch rubber for each propeller, total weight 2 oz.) is in position, the centre of gravity will be further forward, in front of the main plane. The amount of rubber mentioned is for a total weight of 6-1/2 oz. If the weight of the model alone be 6 oz., you will probably have to use 16 strands, which again adds to the weight, and makes one travel in a vicious circle. Therefore I lay emphasis on the advice, Keep down
Comments (0)