Shop Management - Frederick Winslow Taylor (top 10 non fiction books of all time .TXT) 📗
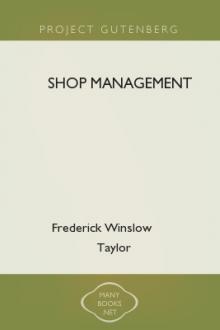
- Author: Frederick Winslow Taylor
- Performer: -
Book online «Shop Management - Frederick Winslow Taylor (top 10 non fiction books of all time .TXT) 📗». Author Frederick Winslow Taylor
a bonus, and (d) differential piece work, has its especial field of
usefulness, and that in every large establishment doing a variety of
work all four of these plans can and should be used at the same time.
Three of these systems were in use at the Bethlehem Steel Company when
the writer left there, and the fourth would have soon been started if he
had remained.
Before leaving this part of the book which has been devoted to pointing
out the value of. the daily task in management, it would seem desirable
to give an illustration of the value of the differential rate piece work
and also of the desirability of making each task as simple and short as
practicable.
The writer quotes as follows from a paper entitled “A Piece Rate
System,” read by him before The American Society of Mechanical Engineers
in 1895:
“The first case in which a differential rate was applied during the year
1884, furnishes a good illustration of what can be accomplished by it. A
standard steel forging, many thousands of which are used each year, had
for several years been turned at the rate of from four to five per day
under the ordinary system of piece work, 50 cents per piece being the
price paid for the work. After analyzing the job, and determining the
shortest time required to do each of the elementary operations of which
it was composed, and then summing up the total, the writer became
convinced that it was possible to turn ten pieces a day. To finish the
forgings at this rate, however, the machinists were obliged to work at
their maximum pace from morning to night, and the lathes were run as
fast as the tools would allow, and under a heavy feed. Ordinary tempered
tools 1 inch by 1 1/2 inch, made of carbon tool steel, were used for
this work.
“It will be appreciated that this was a big day’s work, both for men and
machines, when it is understood that it involved removing, with a single
16-inch lathe, having two saddles, an average of more than 800 lbs of
steel chips in ten hours. In place of the 50 cent rate, that they had
been paid before, the men were given 35 cents per piece when they turned
them at the speed of 10 per day; and when they produced less than ten
they received only 25 cents per piece.
“It took considerable trouble to induce the men to turn at this high
speed, since they did not at first fully appreciate that it was the
intention of the firm to allow them to earn permanently at the rate of
$3.50 per day. But from the day they first turned ten pieces to the
present time, a period of more than ten years, the men who understood
their work have scarcely failed a single day to turn at this rate.
Throughout that time until the beginning of the recent fall in the scale
of wages throughout the country, the rate was not cut.
“During this whole period, the competitors of the company never
succeeded in averaging over half of this production per lathe, although
they knew and even saw what was being done at Midvale. They, however,
did not allow their men to earn from over $2.00 to $2.50 per day, and so
never even approached the maximum output.
“The following table will show the economy of paying high wages under
the differential rate in doing the above job:
“COST OF PRODUCTION PER LATHE PER DAY
ORDINARY SYSTEM OF PIECE WORK—Man’s wages $2.50 Machine cost 3.37 Total
cost per day 5.87 5 pieces produced; Cost per piece $1.17
DIFFERENTIAL RATE SYSTEM—Man’s wages $3.50 Machine cost 3.37 Total cost
per day 6.87 10 pieces produced; Cost per piece $0.69
“The above result was mostly though not entirely due to the
differential rate. The superior system of managing all of the small
details of the shop counted for considerable.”
The exceedingly dull times that began in July, 1893, and were
accompanied by a great fall in prices, rendered it necessary to lower
the wages of machinists throughout the country. The wages of the men in
A. the Midvale Steel Works were reduced at this time, and the change was
accepted by them as fair and just.
Throughout the works, however, the principle of the differential rate
was maintained, and was, and is still, fully appreciated by both the
management and men. Through some error at the time of the general
reduction of wages in 1893, the differential rate on the particular job
above referred to was removed, and a straight piece work rate of 25
cents per piece was substituted for it. The result of abandoning the
differential proved to be the best possible demonstration of its value.
Under straight piece work, the output immediately fell to between six
and eight pieces per day, and remained at this figure for several years,
although under the differential rate it had held throughout a long term
of years steadily at ten per day.
When work is to be repeated many times, the time study should be minute
and exact. Each job should be carefully subdivided into its elementary
operations, and each of these unit times should receive the most
thorough time study. In fixing the times for the tasks, and the piece
work rates on jobs of this class, the job should be subdivided into a
number of divisions, and a separate time and price assigned to each
division rather than to assign a single time and price for the whole
job. This should be done for several reasons, the most important of
which is that the average workman, in order to maintain a rapid pace,
should be given the opportunity of measuring his performance against the
task set him at frequent intervals. Many men are incapable of looking
very far ahead, but if they see a definite opportunity of earning so
many cents by working hard for so many minutes, they will avail
themselves of it.
As an illustration, the steel tires used on car wheels and locomotives
were originally turned in the Midvale Steel Works on piece work, a
single piecework rate being paid for all of the work which could be
done on a tire at a single setting. A fixed price was paid for this
work, whether there was much or little metal to be removed, and on the
average this price was fair to the men. The apparent advantage of fixing
a fair average rate was, that it made rate-fixing exceedingly simple,
and saved clerk work in the time, cost and record keeping.
A careful time study, however, convinced the writer that for the reasons
given above most of the men failed to do their best. In place of the
single rate and time for all of the work done at a setting, the writer
subdivided tire-turning into a number of short operations, and fixed a
proper time and price, varying for each small job, according to the
amount of metal to be removed, and the hardness and diameter of the
tire. The effect of this subdivision was to increase the output, with
the same men, methods, and machines, at least thirty-three per cent.
As an illustration of the minuteness of this subdivision, an instruction
card similar to the one used is reproduced in Figure 1 on the next page.
(This card was about 7 inches long by 4 inches wide.)
[Transcriber’s note — Figure 1 not shown]
The cost of the additional clerk work involved in this change was so
insignificant that it practically did not affect the problem. This
principle of short tasks in tire turning was introduced by the writer in
the Midvale Steel Works in 1883 and is still in full use there, having
survived the test of over twenty years’ trial with a change of
management.
In another establishment a differential rate was applied to tire
turning, with operations subdivided in this way, by adding fifteen per
cent to the pay of each tire turner whenever his daily or weekly piece
work earnings passed a given figure.
Another illustration of the application of this principle of measuring a
man’s performance against a given task at frequent intervals to an
entirely different line of work may be of interest. For this purpose the
writer chooses the manufacture of bicycle balls in the works of the
Symonds Rolling Machine Company, in Fitchburg, Mass. All of the work
done in this factory was subjected to an accurate time study, and then
was changed from day to piece work, through the assistance of functional
foreman ship, etc. The particular operation to be described however, is
that of inspecting bicycle balls before they were finally boxed for
shipment. Many millions of these balls were inspected annually. When the
writer undertook to systematize this work, the factory had been running
for eight or ten years on ordinary day work, so that the various
employees were “old hands,” and skilled at their jobs. The work of
inspection was done entirely by girls—about one hundred and twenty
being employed at it—all on day work.
This work consisted briefly in placing a row of small polished steel
balls on the back of the left hand, in the crease between two of the
fingers pressed together, and while they were rolled over and over, with
the aid of a magnet held in the right hand, they were minutely examined
in a strong light, and the defective balls picked out and thrown into
especial boxes. Four kinds of defects were looked for—dented, soft,
scratched, and fire cracked—and they were mostly 50 minute as to be
invisible to an eye not especially trained to this work. It required the
closest attention and concentration. The girls had worked on day work
for years, ten and one-half hours per day, with a Saturday half-holiday.
The first move before in any way stimulating them toward a larger output
was to insure against a falling off in quality. This was accomplished
through over-inspection. Four of the most trustworthy girls were given
each a lot of balls which had been examined the day before by one of the
regular inspectors. The number identifying the lot having been changed
by the foreman so that none of the over-inspectors knew whose work they
were examining. In addition, one of the lots inspected by the four
over-inspectors was examined on the following day by the chief
inspector, selected on account of her accuracy and integrity.
An effective expedient was adopted for checking the honesty and accuracy
of the over-inspection. Every two or three days a lot of balls was
especially prepared by the foreman, who counted out a definite number of
perfect balls, and added a recorded number of defective balls of each
kind. The inspectors had no means of distinguishing this lot from the
regular commercial lots. And in this way all temptation to slight their
work or make false returns was removed.
After insuring in this way against deterioration in quality, effective
means were at once adopted to increase the output. Improved day work was
substituted for the old slipshod method. An accurate daily record, both
as to quantity and quality, was kept for each inspector. In a
comparatively short time this enabled the foreman to stir the ambition
of all the inspectors by increasing the wages of those who turned out a
large quantity and good quality, at the same time lowering the pay of
those who fell short, and discharging others who proved to be
incorrigibly slow or careless. An accurate time study was made through
the use of a stop watch and record blanks, to determine how fast each
kind of inspection should be done. This showed that
Comments (0)