Shop Management - Frederick Winslow Taylor (top 10 non fiction books of all time .TXT) 📗
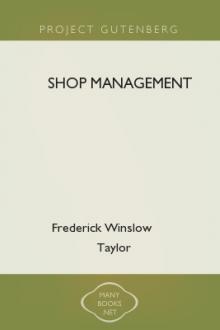
- Author: Frederick Winslow Taylor
- Performer: -
Book online «Shop Management - Frederick Winslow Taylor (top 10 non fiction books of all time .TXT) 📗». Author Frederick Winslow Taylor
“unit times,” and this time study was greatly delayed by having
successively the two leading men who had been trained to the work leave
because they were offered much larger salaries elsewhere. The study of
“unit times” for the yard labor took practically the time of two trained
men for two years. Throughout this time the day and piece workers were
under entirely separate and distinct management. The original foremen
continued to manage the day work, and day and piece workers were never
allowed to work together. Gradually the day work gang was diminished and
the piece workers were increased as one section of work after another
was transformed from the former to the latter.
Two elements which were important to the success of this work should be
noted:
First, on the morning following each day’s work, each workman was given
a slip of paper informing him in detail just how much work he had done
the day before, and the amount he had earned. This enabled him to
measure his performance against his earnings while the details were
fresh in his mind. Without this there would have been great
dissatisfaction among those who failed to climb up to the task asked of
them, and many would have gradually fallen off in their performance.
Second, whenever it was practicable, each man’s work was measured by
itself. Only when absolutely necessary was the work of two men measured
up together and the price divided between them, and then care was taken
to select two men of as nearly as possible the same capacity. Only on
few occasions, and then upon special permission, signed by the writer,
were more than two men allowed to work on gang work, dividing their
earnings between them. Gang work almost invariably results in a failing
off in earnings and consequent dissatisfaction.
An interesting illustration of the desirability of individual piece work
instead of gang work came to our attention at Bethlehem. Several of the
best piece workers among the Bethlehem yard laborers were informed by
their friends that a much higher price per ton was paid for shoveling
ore in another works than the rate given at Bethlehem. After talking the
matter over with the writer he advised them to go to the other works,
which they accordingly did. In about a month they were all back at work
in Bethlehem again, having found that at the other works they were
obliged to work with a gang of men instead of on individual piece work,
and that the rest of the gang worked so slowly that in spite of the high
price paid per ton they earned much less than Bethlehem.
Table 1, on page 54, gives a summary of the work done by the piecework
laborers in handling raw materials, such as ores, anthracite and
bituminous coal, coke, pig-iron, sand, limestone, cinder, scale, ashes,
etc., in the works of the Bethlehem Steel Company, during the year
ending April 30, 1900. This work consisted mainly in loading and
unloading cars on arrival or departure from the works, and for local
transportation, and was done entirely by hand, i.e., without the use of
cranes or other machinery.
The greater part of the credit for making the accurate time study and
actually managing the men on this work should be given to Mr. A. B.
Wadleigh, the writer’s assistant in this section at that time.
TABLE 1. -SHOWING RELATIVE COST OF YARD LABOR UNDER TASK PIECE WORK AND
OLD STYLE DAY WORK
[Transcriber’s note — table 1 omitted]
When the writer left the steel works, the Bethlehem piece workers were
the finest body of picked laborers that he has ever seen together. They
were practically all first-class men, because in each case the task
which they were called upon to perform was such that only a first-class
man could do it. The tasks were all purposely made so severe that not
more than one out of five laborers (perhaps even a smaller percentage
than this) could keep up.
[Footnotes to table 1]
1) It was our intention to fix piece work rates which should enable
first-class workmen to average about 60 per cent more than they had been
earning on day work, namely $1.85 per day. A year’s average shows them
to have earned $1.88 per day, or three cents per man per day more than
we expected—an error of 1 6/10 per cent.
2) The piece workers handled on an average 3 56/100 times as many tons
per day as the day workers.
[end footnotes to table 1]
It was clearly understood by each newcomer as he went to work that
unless he was able to average at least $1.85 per day he would have to
make way for another man who could do so. As a result, first-class men
from all over that part of the country, who were in most cases earning
from $1.05 to $1.15 per day, were anxious to try their hands at earning
$1.85 per day. If they succeeded they were naturally contented, and if
they failed they left, sorry that they were unable to maintain the
proper pace, but with no hard feelings either toward the system or the
management. Throughout the time that the writer was there, labor was as
scarce and as difficult to get as it ever has been in the history of
this country, and yet there was always a surplus of first-class men
ready to leave other jobs and try their hand at Bethlehem piece work.
Perhaps the most notable difference between these men and ordinary
piece workers lay in their changed mental attitude toward their
employers and their work, and in the total absence of soldiering on
their part. The ordinary piece worker would have spent a considerable
part of his time in deciding just how much his employer would allow him
to earn without cutting prices and in then trying to come as close as
possible to this figure, while carefully guarding each job so as to
keep the management from finding out how fast it really could be done.
These men, however, were faced with a new but very simple and
straightforward proposition, namely, am I a first-class laborer or not?
Each man felt that if he belonged in the first class all he had to do
was to work at his best and he would be paid sixty per cent more than
he had been paid in the past. Each piece work price was accepted by the
men without question. They never bargained over nor complained about
rates, and there was no occasion to do so, since they were all equally
fair, and called for almost exactly the same amount of work and fatigue
per dollar of wages.
A careful inquiry into the condition of these men when away from work
developed the fact that out of the whole gang only two were said to be
drinking men. This does not, of course, imply that many of them did not
take an occasional drink. The fact is that a steady drinker would find
it almost impossible to keep up with the pace which was set, so that
they were practically all sober. Many if not most of them were saving
money, and they all lived better than they had before. The results
attained under this system were most satisfactory both to employer and
workmen, and show in a convincing way the possibility of uniting high
wages with a low labor cost.
This is virtually a labor union of first-class men, who are united
together to secure the extra high wages, which belong to them by right
and which in this case are begrudged them by none, and which will be
theirs through dull times as well as periods of activity. Such a union
commands the unqualified admiration and respect of all classes of the
community; the respect equally of workmen, employers, political
economists, and philanthropists. There are no dues for membership, since
all of the expenses are paid by the company. The employers act as
officers of the Union, to enforce its rules and keep its records, since
the interests of the company are identical and bound up with those of
the men. It is never necessary to plead with, or persuade men to join
this Union, since the employers themselves organize it free of cost; the
best workmen in the community are always anxious to belong to it. The
feature most to be regretted about it is that the membership is limited.
The words “labor union” are, however, unfortunately so closely
associated in the minds of most people with the idea of disagreement and
strife between employers and men that it seems almost incongruous to
apply them to this case. Is not this, however, the ideal “labor union,”
with character and special ability of a high order as the only
qualifications for membership.
It is a curious fact that with the people to whom the writer has
described this system, the first feeling, particularly among those more
philanthropically inclined, is one of pity for the inferior workmen who
lost their jobs in order to make way for the first-class men. This
sympathy is entirely misplaced. There was such a demand for labor at the
time that no workman was obliged to be out of work for more than a day
or two, and so the poor workmen were practically as well off as ever.
The feeling, instead of being one of pity for the inferior workmen,
should be one of congratulation and rejoicing that many first-class
men—who through unfortunate circumstances had never had the opportunity
of proving their worth—at last were given the chance to earn high wages
and become prosperous.
What the writer wishes particularly to emphasize is that this whole
system rests upon an accurate and scientific study of unit times, which
is by far the most important element in scientific management. With it,
greater and more permanent results can be attained even under ordinary
day work or piece work than can be reached under any of the more
elaborate systems without it.
In 1895 the writer read a paper before The American Society of
Mechanical Engineers entitled “A Piece Rate System.” His chief object in
writing it was to advocate the study of unit times as the foundation of
good management. Unfortunately, he at the same time described the
“differential rate” system of piece work, which had been introduced by
him in the Midvale Steel Works. Although he called attention to the fact
that the latter was entirely of secondary importance, the differential
rate was widely discussed in the journals of this country and abroad
while practically nothing was said about the study of “unit times.”
Thirteen members of the Society discussed the piece rate system at
length, and only two briefly referred to the study of the “unit times.”
The writer most sincerely trusts that his leading object in writing this
book will not be overlooked, and that scientific time study will receive
the attention which it merits. Bearing in mind the Bethlehem yard labor
as an illustration of the application of the study of unit times as the
foundation of success in management, the following would seem to him a
fair comparison of the older methods with the more modern plan.
For each job there is the quickest time in which it can be done by a
first-class man. This time may be called the “quickest time,” or the
“standard time” for the job. Under all the ordinary systems, this
“quickest time” is more or less completely shrouded in mist. In most
cases, however, the workman is nearer to it and sees it more clearly
than the employer.
Under ordinary piece work the management watch every indication given
Comments (0)