Things To Make - Archibald Williams (the reader ebook .TXT) 📗
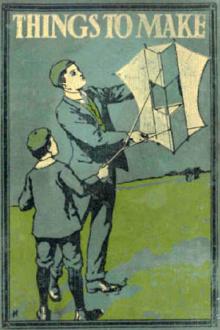
- Author: Archibald Williams
- Performer: -
Book online «Things To Make - Archibald Williams (the reader ebook .TXT) 📗». Author Archibald Williams
The eccentric may be built up from a metal disc about 3/4 inch diameter and two slightly larger discs soldered concentrically to the sides. The width of the middle disc should be the same as that of the eccentric rod. A careful filer could make a passable eccentric by sinking a square or semicircular groove in the edge of a wide disc. The centre of the eccentric must be found carefully, and a point marked at a distance from it equal to half the travel of the valve. To ascertain this, pull the valve forward until the steam port is fully exposed, insert a bar at the rear end of the valve tube, and mark it. Then push the valve back until a wire pushed through the port from the cylinder side shows that the port is again fully exposed. Insert and mark the bar again. The distance between the marks gives you the "travel" required.
Order of Assembly.—The following list of operations in their order may assist the beginner:
Make the bed.
Cut out cylinder barrel, piston, and valve tube.
Bevel off the ends of the last inside to allow the valve to enter easily.
Make the valve.
Bore the steam ports, and solder valve tube and cylinder together.
Solder holding-down wing, W, to cylinder.
Finish off the piston.
Solder the bearings in their standards.
Prepare shaft, crank disc, crank pin, and piston rod.
Fix the cylinder to the bed, in which a slot must be cut for the wing and holding-down bolt.
Attach the piston rod to the piston, and insert piston in cylinder.
Bore hole for shaft in centre of crank disc, and another, 9/16 inch away (centre to centre), for crank pin.
Solder in crank pin squarely to disc.
Pass shaft through bearings and slip on the crank disc.
Pass front end of piston rod over the crank pin.
Lay bearing standard on bed squarely to the centre line of the cylinder, turn crank fully back, and move the standard about till the back end of the piston clears the back end of the cylinder by about 1/32 inch.
Get standard quite square, and adjust sideways till connecting rod is in line with axis of cylinder.
Mark off and screw down the standard.
Make the eccentric, eccentric rod, and strap. Slip eccentric on shaft.
Put valve in position and draw it forward till the port is exposed.
Turn the eccentric forward, and mark the rod opposite centre of valve pin.
Bore hole for pin, and insert pin.
Hold the crank shaft firmly, and revolve eccentric till the port just begins to open on its forward stroke. Rotate crank disc on shaft till the crank pin is full forward.
Solder eccentric and disc to shaft.
Solder steam pipe to cylinder, and a brass disc to the rear end of the cylinder.
Fit a fly wheel of metal or wood. This must be fairly heavy, as it has to overcome all friction during the return or exhaust stroke.
Action of Engine.—During the forward motion of the piston the valve is pushed back by the eccentric until the steam port is fully opened, and is then drawn forward, covering the port. At the end of the power stroke the port has begun to open to the air, to allow the steam to escape throughout the exhaust stroke, in the course of which the valve is pushed back until, just at the end of the stroke, the steam port begins to open again.
Notes.— (l.) The connecting rod may be made shorter than shown in Figs. 51 and 52; but in that case the piston also must be shortened to allow for the greater obliquity of the rod at half-stroke.
(2.) If two opposed cylinders are made to operate the one crank, a double-acting engine is obtained. Both valves may be operated by a single eccentric, the connecting rod of one being pivoted to a small lug projecting from the eccentric strap. If three cylinders are set 120 degrees apart round the crank shaft, a continuous turning effect is given. This type will be found useful for running small dynamos.
(3.) If it is desired to use the exhaust steam to promote a draught in the boiler furnace, it should be led away by a small pipe from the rear end of the valve tube.
XV. A HORIZONTAL SLIDE-VALVE ENGINE.The reader who has succeeded in putting together the simple engine described in the preceding chapter may wish to try his hand on something more ambitious in the same line. The engine illustrated in Figs. 53 to 66 will give sufficient scope for energy and handiness with drill and soldering iron. The writer made an engine of the same kind, differing only from that shown in the design of the crosshead guides, without the assistance of a lathe, except for turning the piston and fly wheel—the last bought in the rough. Files, drills, taps, a hack saw, and a soldering iron did all the rest of the work.
Solder plays so important a part in the assembling of the many pieces of the engine that, if the machine fell into the fire, a rapid disintegration would follow. But in actual use the engine has proved very satisfactory; and if not such as the highly-skilled model-maker with a well-equipped workshop at his command would prefer to expend his time on, it will afford a useful lesson in the use of the simpler tools. Under 50 lbs. of steam it develops sufficient power to run a small electric-lighting installation, or to do other useful work on a moderate scale.
[Illustration: Fig. 53.—Elevation of a large horizontal engine.]
The principal dimensions of the engine are as follows:
Bedplate (sheet zinc), 13-1/2 inches long; 4-1/2 inches wide; 1/8 inch thick.
Support of bedplate (1/20 inch zinc), 3 inches high from wooden base to underside of bedplate.
Cylinder (mandrel-drawn brass tubing), 1-1/2 inches internal diameter; 2-13/16 inches long over all.
Piston, 1-1/2 inches diameter; 1/2 inch long.
Stroke of piston, 2-1/4 inches.
Connecting rod, 5 inches long between centres; 5/16 inch diameter.
Piston rod, 5-1/8 inches long; 1/4 inch diameter.
Valve rod, 4-1/8 inches long; 3/16 inch diameter.
Crank shaft, 5 inches long; 1/2 inch diameter.
Centre line of piston rod, 1-1/4 inches laterally from near edge of bed; 1-5/8 inches from valve-rod centre line; 1-5/8 inches vertically above bed.
Centre line of crank shaft, 10-3/8 inches from cross centre line of cylinder.
Bearings, 1 inch long.
Eccentric, 9/32-inch throw.
Fly wheel, diameter, 7-1/2 inches; width, 1 inch; weight, 6 lbs.
Pump, 3/8-inch bore; 3/8-inch stroke; plunger, 2 inches long.
[Illustration: Fig. 54.—Plan of a large horizontal engine.]
Other dimensions will be gathered from the various diagrams of details.
The reader will, of course, suit his own fancy in following these dimensions, or in working to them on a reduced scale, or in modifying details where he considers he can effect his object in a simpler manner.
The diagrams are sufficiently explicit to render it unnecessary to describe the making of the engine from start to finish, so remarks will be limited to those points which require most careful construction and adjustment.
[Illustration: Fig. 55.—Standards of Bedplate.]
The Bedplate.—This should be accurately squared and mounted on its four arch-like supports. (For dimensions, consult Fig. 55.) Half an inch is allowed top and bottom for the turnovers by which the supports are screwed to the bedplate and base. The ends of the longer supports are turned back so as to lie in front of the end supports, to which they may be attached by screws or solder, after all four parts have been screwed to the bed. Care must be taken that the parts all have the same height. Drill all holes in the turnovers before bending. Use 1/8-inch screws. Turn the bed bottom upwards, and stand the four supports, temporarily assembled, on it upside down and in their correct positions, and mark off for the 3/32-inch holes to be drilled in the bed. A hole 3/4 inch in diameter should be cut in the bedplate for the exhaust pipe, round a centre 2 inches from the end and 1-5/8 inches from the edge on the fly-wheel side, and two more holes for the pump.
Making the Cylinder Slide and Valve.—The cylinder barrel must be perfectly cylindrical and free from any dents. Mandrel-drawn brass tubing, 1/16-inch thick, may be selected. If you cannot get this turned off at the ends in a lathe, mark the lines round it for working to with the aid of a perfectly straight edged strip of paper, 2-13/16 inches wide, rolled twice round the tube. The coils must lie exactly under one another. Make plain scratches at each end of the paper with a sharp steel point. Cut off at a distance of 1/16-inch from the lines, and work up to the lines with a file, finishing by rubbing the ends on a piece of emery cloth resting on a hard, true surface.
[Illustration: FIG. 56.-Cylinder standard before being bent.]
A square-cornered notch 1/8 inch deep and 7/8 inch wide must now be cut in each end of the barrel, the two notches being exactly in line with one another. These are to admit steam from the steam ways into the cylinder.
Cylinder Standards.-Use 5/64 or 3/32 inch brass plate for these. Two pieces of the dimensions shown in Fig. 56 are needed. Scratch a line exactly down the middle of each, and a cross line 1/2 inch from one end. The other end should be marked, cut, and filed to a semicircle. Drill three 3/16-inch holes in the turnover for the holding-down screws. The two standards should now be soldered temporarily together at the round ends and trued up to match each other exactly. Place them in the vice with the bending lines exactly level with the jaws, split the turnovers apart, and hammer them over at right angles to the main parts. Whether this has been done correctly may be tested by placing the standards on a flat surface. Take the standards apart, and scratch a cross line on each 1-5/8 inch from the lower surface of the foot on the side away from the foot. Make a punch mark where the line crosses the vertical line previously drawn, and with this as centre describe a circle of the diameter of the outside of the barrel. Cut out the inside and file carefully up to the circle, stopping when the barrel makes a tight fit. On the inside of the hole file a nick 1/8 inch deep, as shown in Fig. 56. Remember that this nick must be on the left of one standard and on the right of the other, so that they shall pair off properly.
Standards and barrel must now be cleaned for soldering. Screw one standard down to a wood base; slip one end of the barrel into it; pass the other standard over the other end of the barrel, and adjust everything so that the barrel ends are flush with the, outer surfaces of the standard, and the nicks of the barrel in line with the standard nicks. Then screw the other standard to the base. Solder must be run well into the joints, as these will have to stand all the longitudinal working strain.
The next step is the fitting of the cylinder covers. If you can obtain two stout brass discs 2-1/8 inches in diameter, some trouble will be saved; otherwise you must cut them out of 3/32-inch plate. The centre of each should be marked, and four lines 45 degrees apart be scratched through it from side to side. A circle of 15/16-inch radius is now drawn to cut the lines, and punch marks are made at the eight points of intersection. Solder the covers lightly to the foot side of their standards, marked sides outwards, and drill 1/8-inch holes through cover and standard at the punch marks. Make matching marks on the edges. Unsolder the covers, enlarge the holes in them to take 5/32-inch screws; and tap the holes in the standards. This method will
Comments (0)